Neyveli,
home of the Neyveli Lignite Corporation, is India’s energy-bridge to the
21st century and a fulfillment of Pandit Nehru’s vision.
Incidentally, Nehru and NLC share a common birthday (14.11.1956). Nehru
launched the mining operations with his golden touch in May 1957. Ever
since, there has been no looking back. NLC has achieved the objectives it
has set for itself, fulfilling its corporate mission to be the leader in the
industry. Comprising of two open cast mines, two Pithead Thermal Power
stations, Briquetting & carbonization plant and a fertilizer plant,
NLC’s growth is sustained and its contribution to India’s social and
economic development is significant.
Mine-I
Demarcated over an area of 16.69sq.kms., with a reserve of about 287 million
tonnes, Mine-I is situated on the northern part of the field adjacent to the
Neyveli township. The lignite seam was first exposed in august 1961 and
regular lignite mining was commenced in May 1962. Its production (6.5
million tonnes of lignite per annum) feeds thermal power station-I,
briquetting & carbonization plant and the process steam plant.
While the overburden
thickness varies from 70 to 95m., the lignite thickness is 10 to 23m. German
excavation technology in open cast mining, using bucket wheel excavators,
conveyors and spreaders was used in this mine for the first time in the
country. A huge reservoir of ground water exists below the entire lignite
bed, exerting an upward pressure of 6 to 8 kg/sq.cm., which is tackled by an
effective ground water management system.
TOP
Mine-II
Mine-II is located 5kms
South of mine-I spread over an area of 26sq.kms., with 398 million tonnes
reserve. The lignite seam was first exposed in September 1984 and regular
lignite mining commenced in March 1985. The maximum overburden is 103m and
the lignite thickness varies from 8 to 22m. Initially, the mine was started
with a production capacity of 4.7 million tonnes and in February’83 the
capacity was enhanced to 10.5 million tonnes per annum. The lignite
production in this mine meets the fuel requirement of thermal power
station-II. The method of mining and equipment used are similar to that of
mine-I.
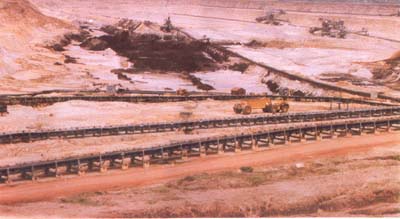
TOP
Thermal
power station-I
An epitome of indo-soviet
collaboration, Neyveli thermal power station-I (TPS-I) was commissioned with
one unit of 50mw in may 1962. Presently, this power station has six units of
50 mw each and three units of 100 mw each.
The unique features of this
power station:
- First
lignite-fired thermal power station in south east Asia.
- First
pit head thermal power station in India
- First
largest thermal power station in south India.
- Continuously
achieving over 70% plant load factor, from 1982-83 to 1991-92 against
the national average of around 50% and has continuously bagged the
meritorious productivity award instituted by the department of power,
government of India.
The power generated from
this thermal power station is fed to the grid of TamilNadu electricity
board, the sole beneficiary.
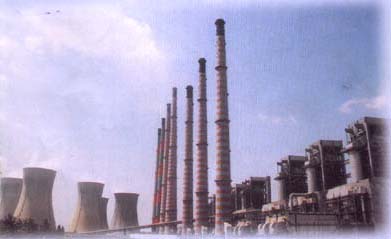
TOP
Thermal
power station-II
Thermal power station-II (TPS-II)
has been a major source of power to all southern states of India. The 1470
mw capacity power station consists of 7 units of 210 mw each. The first unit
was synchronized in March 1986. The second unit of this power station was
formally commissioned by the then prime minister shri. Rajiv Gandhi. This
power station has seen a series of technological innovations such as:
- Largest
lignite-fired thermal power station in India
- First
and tallest tower type boiler in the country (92.7m. height)
- First
software based burner management system
- First
hydrogen/hydrogen-cooled generator of this size.
- First
boiler to be cleaned by hydrofluoric acid
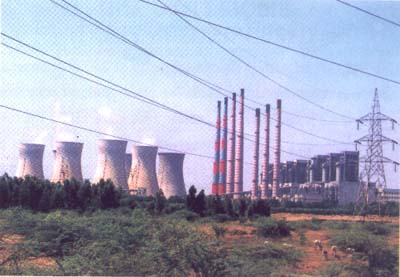
TOP
Fertilizer
Plant
13.7 Fertilizer Plant with
an installed capacity of 1.52 lakh tonnes of Urea per annum was
commissioned in 1966. The equipment of the Fertilizer Plant were supplied by
M/s. PINTSCH PAMAG,
M/s. Linde of West Germany and M/s. Ansaldo of Italy. Initially the
plant used raw lignite as feedstock. However, due to certain operational and
technological constraints, the
plant was switched over to Low Sulphur Heavy Stock/Furnace
Oil as feedstock since July 1979.
TOP
Briquettting
and Carbonization Plant
13.8 Briquetting and Carbonization
Plant was commissioned in 1966 with an installed capacity
of 3.27 LT of Carbonized briquettes (Leco) per annum. The equipment were
supplied by consortium of West
German firms. The achievable capacity has been subsequently
assessed as 2,62,000 Tonne of Coke per annum. Coke is used in Electro
chemical, Electro
metallurgical industries as a reductant and in tea sector as a versatile
fuel for drying and also as
substitute for coal, in cement and paper industries. In the process
of low temperature carbonization adopted in the plant base chemicals vital
to the chemical
industries viz. Carbolic acid, Orthocresol, Metaparacresol, Xylenol,
Multivalent phenol and
neutral oil are also produced.
The plant is under temporary suspension since 5th April 2001 owing to
inadequate market
demand. The plant is about to be relinquished by NLC.
TOP
|